Industry 4.0 is a reality that cannot be ignored these days, and is emerging as a major development in modern industry. This new era in industry is characterised by the digitalisation of processes, artificial intelligence and automation. Faced with these advances, companies are faced with a host of challenges if they are to remain competitive and sustainable in a constantly evolving market.
The first challenge of Industry 4.0 is to adopt digital processes. Companies must be able to collect, process and analyse data to improve their production processes and boost productivity. The use of sensors, the Internet of Things and data analysis are key tools for achieving this. Collecting data enables production processes to be monitored and optimised, breakdowns to be detected before they occur and future production requirements to be forecast.
The second challenge is to implement automation systems for repetitive, low added-value tasks. Collaborative robotics, cobots, AGVs (automated guided vehicles) and other automation technologies enable companies to reduce costs and increase the quality of production. Cobots can work alongside human workers, freeing them from repetitive and dangerous tasks.
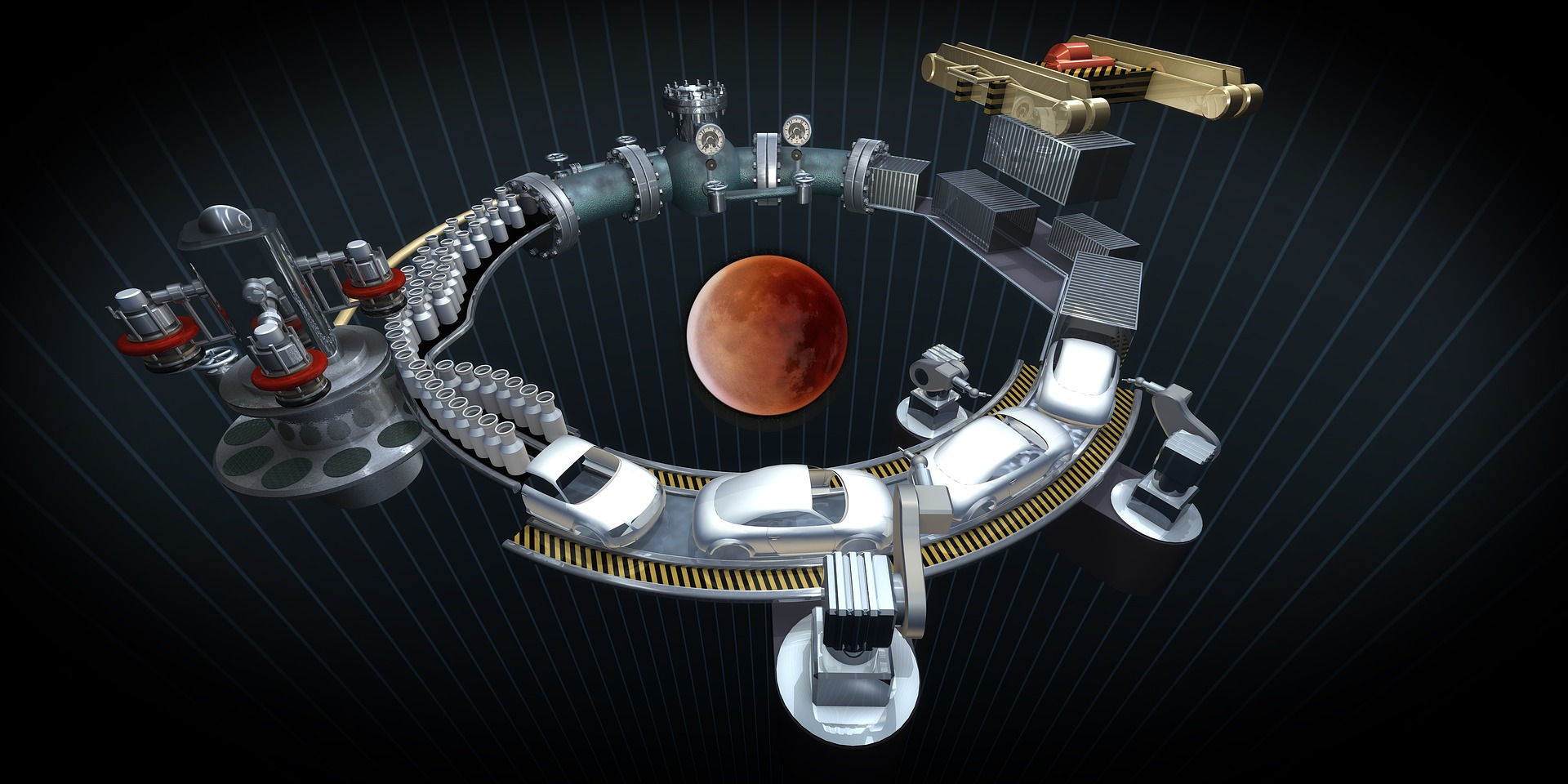
The third challenge is to implement artificial intelligence processes to improve production quality, optimise predictive maintenance and forecast market trends. Machine learning algorithms can optimise production processes by identifying errors and quality problems, while predictive maintenance can predict machine breakdowns and avoid costly downtime.
In conclusion, Industry 4.0 represents a major challenge for companies, but it is also an opportunity for them to modernise and become more competitive in the marketplace. The digitalisation of processes, automation and artificial intelligence are the key elements of this transformation. Companies that are able to meet these challenges and adapt quickly to changes in the market will be the most competitive and successful in the Industry 4.0 era.